Choosing a Bin Vent Filter for Your Steel Mill Process
If you own or work in a steel mill, you’re around process equipment that requires dust filtration. Storage silos, bucket elevators, conveyor transfer and discharge points all generate large volumes of dust, typically hazardous if uncontained. What are the considerations when selecting the right bin vent filter for your operation? Let’s take a look.
As the name implies, a bin vent filter releases clean air from a storage device or mill conveying process that generates dust. In this case, containment doesn’t mean collecting the dust, but rather separating and reclaiming it as useful dry bulk material. Steel mills commonly use powders like lime and carbon, which are potential health hazards. Poor filtration results in harmful fugitive dust escaping into the atmosphere. This puts workers and others at risk in addition to polluting the environment. Also, you’re likely aware that lime is corrosive and can damage your equipment.
Storage silos can be especially hazardous because they are susceptible to overpressurization. One way that this can occur is when the filter media in a bin vent housing clogs up. Pressure builds as the bulk material continues to fill a silo but displaced air cannot escape fast enough. When the weakest part of the structure gives way, serious volumes of bulk material can escape. Besides polluting the environment, an event like this can also endanger lives, especially those nearby. Debris from structure failure can include the filter housing itself blowing off the roof.
Bin Vent Filter Selection Checklist
Here are eight things to consider when comparing different brand options for purchase or drafting your bin vent filter specification.
1. Filter Type and Configuration
Bag filter or pleated cartridge bin vent? Does it matter where the filters are accessed? Answers depend on where the unit installation will be and what you’re willing to tolerate with filter changeout challenges.
The limitation with bag filters is that they are in top-access or bottom-access housing designs. Access from the bottom pretty much excludes using them on most bucket elevators, discharge conveyors, and conveyor transfer point setups. Installation on top of a silo roof means personnel must enter the silo itself, risking those inherent dangers.
Top-access units are awkward for long bag and even shorter pleated cartridge filter maintenance, especially at elevated heights. Imagine handling steel-supported bags 8 to 30 feet long while being lifted 20 to 100+ feet up in the air. Top-access pleated cartridge units are complex, requiring disassembly and reassembly of multiple components. That includes the filter, collars, hold-down brackets, and even the venturi!
Pleated cartridge bin vents with front filter access have key advantages. Changing them out is far easier and safer, especially from a boom lift. (With SMAC bin vents, you don’t even have to enter the filter housing.) Pleated cartridge filters have much more media area than bag filters. It’s the pleating that permits their short length and thus, compact housings. More media area allows considerably more airflow through the bin vent.
2. Construction
First, ensure that the bin vent filter you’re considering meets combustible dust standards. NFPA 652 is the Standard on Combustible Dust and breaks this down, but work with a supplier’s expert. They must also be knowledgeable about explosion venting and OSHA-approved service platforms with ladders.
Don’t settle for cheap construction just because it’s a machine you must have but doesn’t actually produce a product. Do you want it to hold up for the long haul, or replace it in 10 years or less? Look for 10-gauge steel construction minimum (SMAC uses 7 & 10 gauge). Insist on a welded housing without bolt holes to prevent leaks and rust. Units installed outdoors commonly have water puddling on the roof from rain or snow. So, choose a housing with a sloping roof.
Narrow the choices by specifying powder coating, which provides a long-lasting finish that’s tougher and thicker than conventional paints. Don’t accept a paint finish that will soon crack, flake, and allow rust to settle in and spread.
3. Filtration Efficiency
We discussed filter types and media area earlier, but you must examine filtration efficiency as well. Bin air filters in your steel mill must meet government air quality standards for particulate matter. You’ll find that filter media efficiencies vary, typically between MERV 10 and MERV 15:
- MERV 10 efficiency is 85% or better on average particle size 3.0-10.0 micron, and 50% – 64% on average particles size 1.0-3.0 micron.
- MERV 15 efficiency is 90% or better on average particle size 1.0-3.0 micron, and 85% – 94% on average particle size 0.3-1.0 micron
(SMAC filters are also available with MERV 16 efficiency, which is 90% or better on average particle size 1.0-3.0 micron and 95% or better on 0.3-1.0 micron.)
Nanofiber technology offers the highest efficiency in filter media. Look for a range of high-efficiency filter media options to suit your dust types. Caution: Some bin vent brands only work on large, coarse particles. Don’t take filtration efficiency for granted when evaluating brands. Learn more about SMAC filters and their efficiencies.
4. Cleaning Technology
Bin vent options on the market today have some method for cleaning the filters without having to remove them. Most use forced air and some old designs still clean by mechanical shaking. Let’s focus on the air-cleaned types.
Reverse Flow vs. Reverse Pulse-jet
Baghouses primarily use reverse flow filter cleaning. A fan rotates over the bags, continuously blowing air down into their clean side to dislodge caked dust. This low-pressure air cleans a few filters at a time so filtration never stops. This requires no compressed air, which is an advantage. Some baghouses that use pleated bags do use compressed air for more effective pulse cleaning of the filters.
Almost all pleated cartridge filter units use reverse pulse-jet cleaning. Strong and controlled pulses of compressed air are directed inside the filters. This effectively blows most of the accumulated dust off the outside. As with the reverse flow method, only a few filters pulse clean at a time so filtration is continuous.
Pulse Cleaning Control
The cleaning frequency and amount of compressed air usage per pulse are programmed on a solid-state controller. A predictably constant operation of material transfer and silo filling might call for just a continuous timer controller. This is powered on and off along with the processing equipment. Be aware that continuous pulsing of the bin air filters will wear the filters faster than when cleaning is only needed.
An on-demand controller constantly monitors the state of the filters and pulses them clean as required. This extends the life of the filters by greatly reducing wear on them due to the pulsing. It also lowers wear on the solenoid and diaphragm valves. It’s energy-efficient as well since it consumes less compressed air. Overall, system efficiency is maximized when an on-demand controller is chosen. Plus, you never know when operational conditions will change.
5. Filter Changeout Pitfalls
We already talked about the awkwardness of top-access and bottom-access bin vent filter designs. So, are there any differences between front-access models that you should know about? Yes! All front-access, filter slide-in rail systems are not the same. In poorly designed systems, here are a few things that can go wrong when changing out the filters.
Ramping pans
The top pans of filter cartridges can slide over each other during installation if there’s no provision to prevent it. This happens when an installer pushes the new filter in by the filter media body, causing the filter to tilt up. The pan ramps on top of the filter behind it and it’s often not noticed. When the rails are forcibly clamped closed, the pan gasket doesn’t seal against the tube sheet. This results in dust bypassing the filter.
Misaligned filters
Even if the filter pans don’t ramp on top of each other, some designs fail to properly align them to their corresponding holes in the tube sheet. This will negatively affect pulse cleaning, and even permit filter bypass if the pan gaskets overlap the tube sheet holes.
Improper grounding
Filter cartridges need to be grounded to dissipate static charge buildup inside the housing, especially for combustible dust. Some bin vent designs have unreliable methods to achieve this. Models with dubious procedures that require installers to take extra steps and make an extra effort should be avoided.
Unsealed gaskets
Procedures and training are fine, but filter installers are human. They can properly slide all the filters into position but then forget to clamp them to the tube sheet. The result is total filter bypass. Choose a bin vent with a fail-safe system. (SMAC has a feature that will not allow the door to close unless the filters are securely clamped in position.)
Also, beware of so-called flexible designs that attempt to accept generic filter cartridges “for your convenience.” Filter alignment and the integrity of the seals are certainly suspect. (Side note: Knock-off filters may be inexpensive upfront. However, frequent changeout and construction failures will cost you more in the long run. Separation of gaskets and the filter media itself from the end pans is far too common.)
6. Installation
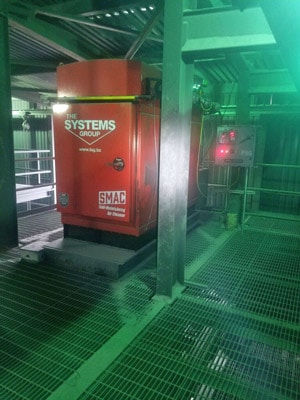
Bin vent filter installation on top of a small indoor silo located under the floor
Select a bin vent filter that’s completely preassembled and ready to install. Doing so will curtail erection costs and avoid unsatisfactory field assembly. Ask what the mating flange options are for direct mounting, which requires no ductwork. Choose a supplier that’s flexible and works with you on planning.
7. Maintenance
Obviously, you’ll want to pick a bin vent that does not require frequent maintenance to keep it operational. This will save you time and money, and minimize shutdowns as well. Units that have no moving parts inside the housing will be the most trouble-free.
Proper filter selection for your mill’s dust application will maximize filter life so changeout won’t be needed for years. When considering a supplier, ask them what the expected filter life will be to avoid surprises and unexpected costs.
Self-maintaining systems are the best, but solenoid and diaphragm valves might occasionally need replacing. So, keep spares on hand. It’s not advisable to continue loading up filters with dust beyond their programmed cleaning cycles. Verify that the pulsing system can be checked without having to shut down the unit and your process equipment.
As previously mentioned, a solidly built bin vent unit will stand up to continuous use and weather for many years. Choose heavy-duty, welded construction (without rusting bolt holes), a sloping roof, and long-lasting powder coat paint.
8. Warranty
Finally, compare manufacturers’ warranties and read the fine print! Typically, the coverage periods for the housing structure, filters, and accessories will vary within a single supplier’s warranty. Don’t settle for a vague warranty statement about a certain number of years. Check if any maintenance requirements are specified which, if not met, may void a warranty.
Conclusion
Use the above information to help you choose a bin vent filter that’s right for your steel mill’s dust-generating process. Whether you need a silo bin vent or multiple units for your material conveying line, these guidelines will help you decide. But be sure to work with an expert.
We here at The Systems Group have dust collection applications experts and fully trained field crews. Our employees make the difference. We pride ourselves on the quality, efficiency, and durability of our SMAC Bin Vents and the service we provide. Contact us today!