SOLUTION: ELECTRICAL ROOM PRESSURIZATION
POSITIVE PRESSURE
The SMAC industrial air cleaner was designed specifically for the harsh environment found in and around steel mills. SMAC room pressurization is the most efficient, cost-effective, and lowest maintenance solution for keeping critical spaces clean.
Traditional room filtration involves a bank of HVAC filters that needs to be changed weekly or even daily to ensure the mill’s employees and equipment remain protected from harmful or conductive dust. These frequent changes can add up to a lot of money spent on labor and filter media.
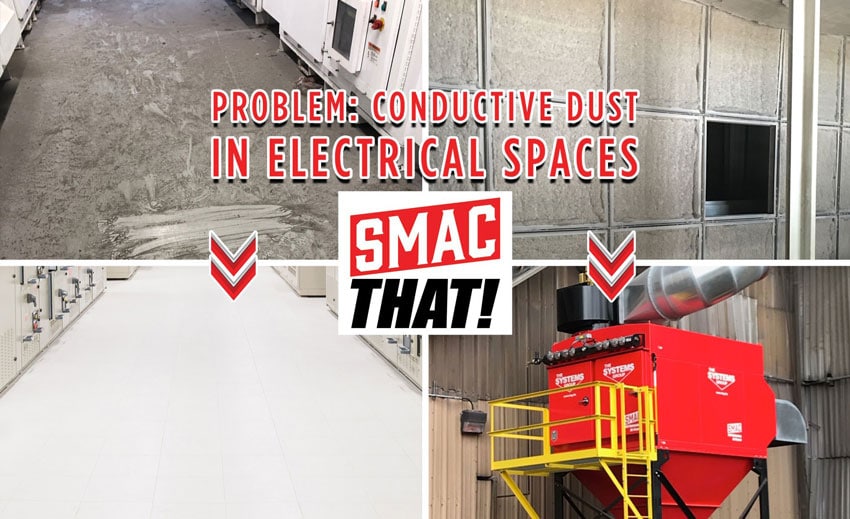
So How Does Room Pressurization Work?
Opening a door and not feeling air coming out, or even worse, the air being pulled in with negative pressure, is a problem.
Room pressurization with positive clean air keeps conductive dust and other harmful contaminants out! SMAC does this by forcing enough clean air into the room that it is impossible for dust to enter. You can tell when a room has positive pressure if you open a door and can feel air coming out.
Room Pressurization Applications
SMAC is the solution for many room pressurization applications commonly found in steel mills. Systems has a long line of successful transformer vault SMAC unit installations. Our SMAC systems are in place protecting EAF and LMF transformer vaults across the country, eliminating conductive dust and arc flash.
The SMAC unit can be sized for any single MCC room or even multiple MCC rooms. The SMAC comes in many different variations. It is modular in design so making a standard model custom is an easy task for any size room. An MCC room pressurization system couldn’t be simpler.
At Systems, we believe Safety is JOB ONE, which includes the air we all breathe. SMAC units can provide HEPA grade filtration to operator pulpits anywhere in your mill, protecting your employees.
A Closer Look At…
SMAC MINI for Crane Cab Filtration
SMAC MINI Features
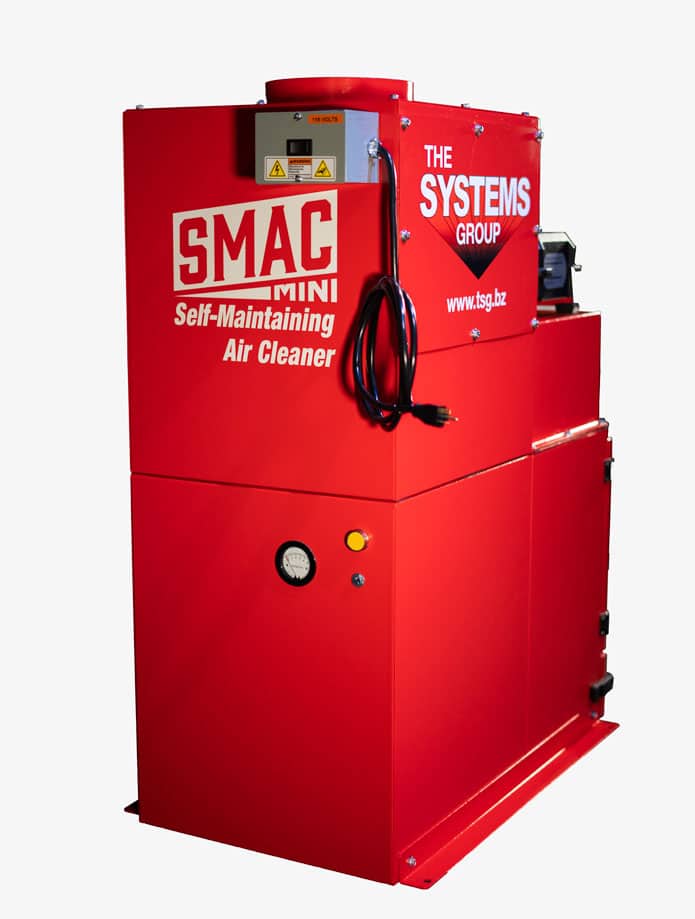
SMAC vs. HVAC Room Pressurization Systems
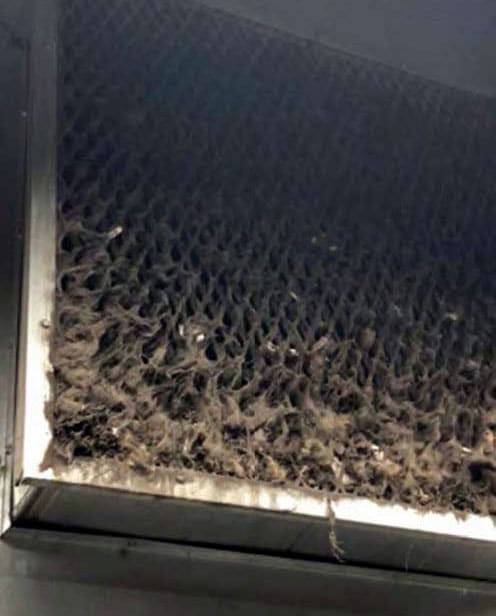
What type of room pressurization equipment is best? Fans with heating, ventilation, and air conditioning (HVAC) filters have traditionally been used but are they the right choice today? Which room air pressurization systems are ideal for steel mill applications like MCC electrical rooms?
While most steel mills use HVAC systems in an attempt to keep areas clean, this is inefficient and ineffective because these types of filters are not able to catch all of the dust particles. When these filters have dust on them it increases the static pressure resistance on the HVAC system and can reduce the amount of positive pressure in the room.
HVAC systems with standard filters are typically rated MERV 5. However, this type of system is not ideal for use in a steel mill. The airborne dust load in a typical steel mill is very high. Standard HVAC filters are not designed to deal with this type of dust load. They will quickly become overwhelmed with dust and will start to block airflow through the system as well as allowing smaller dust particles through the filters.
Also, it is common for the HVAC filters to require changing once a week or even once a day. Besides the expense of constant filter changes, steel mills also must deal with the time and labor required to change these filters. Further, the cost of disposal must be handled since the filters may contain hazardous materials.
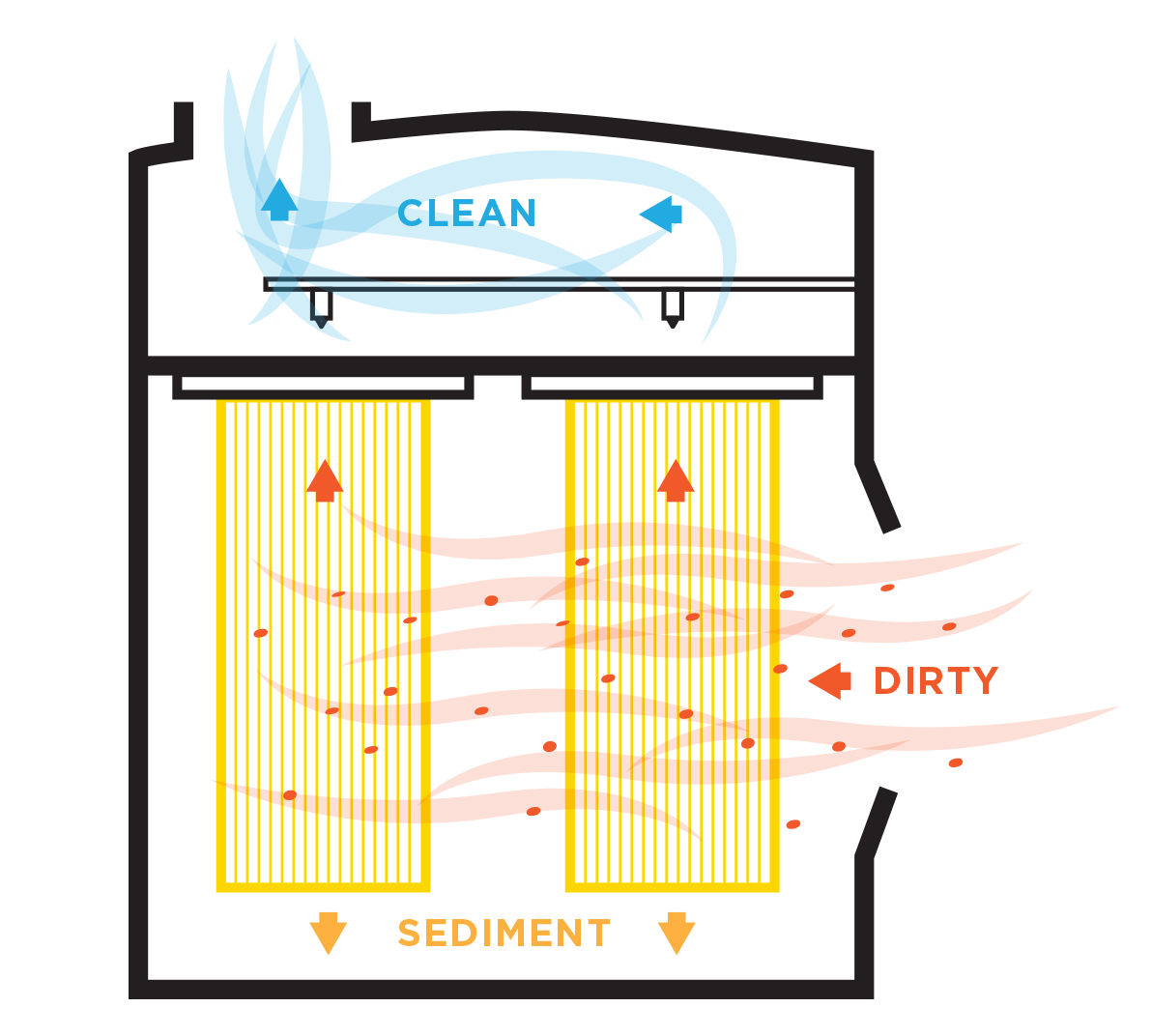
Better Than HVAC
Instead of HVAC or HEPA filters, SMAC uses round cartridge filters that hang vertically from a tube sheet. It’s called “self-maintaining” because its filters are cleaned by pulses of compressed air. As a result, they do not require manual cleaning. By using positive pressure from SMAC, critical spaces in steel mills can be kept clean at a much lower cost and with better results. It’s the forefront room pressurization unit for steel mills.